Ultrasound
Sonotrodes/horns
We manufacture ultrasonic sonotrodes, also known as horns, according to customer specifications using the most precise CAD/CAM technology. The amplitude distribution and longevity of sonotrodes/horns are greatly increased by choosing the right metals – such as steel, titanium or aluminum. These can be treated with various coatings, e.g. to increase resistance to wear. During construction, we calculate the optimal oscillation behavior of the sonotrodes according to the finite element method (FEM). We then test and document the amplitude distribution on the finished product using the latest laser measuring techniques.

Versions
- Welding sonotrodes
- Cleaning sonotrodes
- Cutting sonotrodes
- Drilling sonotrodes
- Screening sonotrodes
FAQ
Since the speed of sound varies depending on the material, sonotrodes vary in height. This may mean that sonotrodes made of e.g. titanium and steel have different dimensions. Our team of experts is happy to help you size and design sonotrodes using a wide range of materials to find the ideal design for your application.
We offer various coatings for titanium. Depending on the area of application, coatings can be used e.g. to increase the sonotrodes' resistance to wear. Our product range includes a coating whose surface is harder than hardened steel.
In most cases, ultrasonic sonotrodes are made from titanium – of various qualities – or steel. In rare cases, aluminum is used. This is particularly useful for test sonotrodes and applications that require rapid heat dissipation. For cutting textiles, we primarily use steel. The choice of material depends on the area of application, the customer requirements and the durability of the sonotrode, as well as the cost, of course.
Since each sonotrode is developed and manufactured for a specific customer, our team of experts is available to advise you at any time.
Depending on the type of steel, different degrees of hardness are possible.
No, each sonotrode is developed and manufactured by our team of specialists especially for the customer so that it meets the specific requirements of the application. For this reason, we require information from you in advance about the material to be processed and about the welding or cutting surface.
In principle, sonotrodes are wear parts. The degree of wear of a tool can be caused by different factors and may vary from application to application.
Three main factors affect the degree of wear:
- Material of the sonotrode and treatment of the material (e.g. whether the sonotrode was hardened)
- Operating time/area
- Was the welding stack correctly designed and constructed? Incorrect design can result in cracks and premature wearing of the sonotrode.
We use special threaded bolts and adapter screws to connect the sonotrodes to the system components. The sonotrode is connected to either the converter or the booster. In addition, we are happy to offer suitable feed units for the mounted system components.
Contact our
team of experts!
Our team of experts is happy to help you find the best solution for your project. Simply fill out the following contact form and a member of our sales team will be in touch.
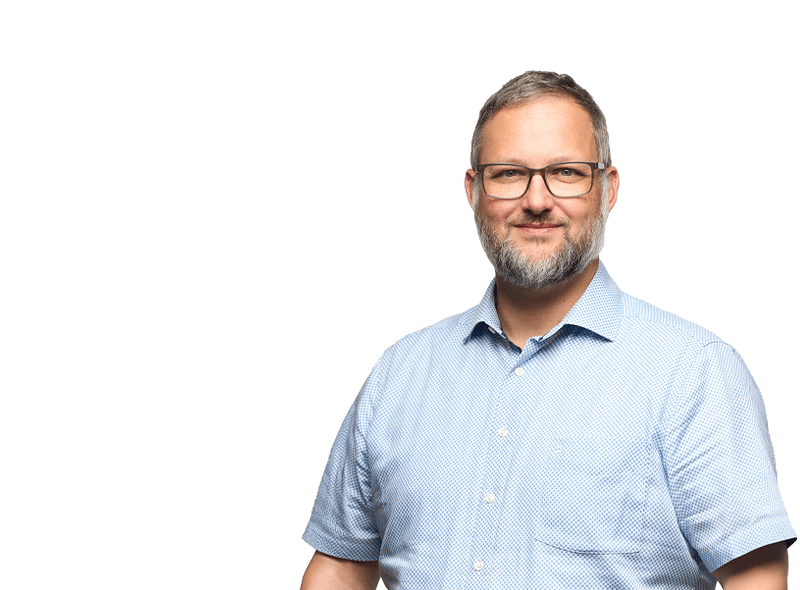